Water Jet Cutting
Advantages of Water Jet Cutting
Industries Served
Comparison Chart
Materials Cut
Hy-Grade Metal Products is proud to announce the purchase of a Koike Aronson 5’ x 10’ Water Jet cutting table.
We offer a competitive cost for prototypes, limited or production runs on short notice. Precise and intricate shapes with tolerances of +/-.005” can easily be achieved. Water jet cutting produces no to very little burr, no stresses to the material, and does not temper or heat effect the cutting zones. In most cases, there is no need for secondary processing.
We can take your .DXF files, CAD files, or scanned images and quickly turn them into finished products. Our nesting program will assure maximum yield of your product from the material used.
Our water jet can cut virtually any material. Metals, composites and several other materials can be processed to your exacting needs with very little lead times.
Examples of Materials
Metals
- Aluminum
- Armor Plate
- Brass
- Bronze
- Cast Iron
- Copper
- Exotic – Gold, silver, etc
- Hastelloy
- Inconel
- Molybdenum
- Monel
- Nickel Alloys
- Stainless Steel
- Steel – Hardened
- Steel – Mild
- Steel – Spring
- Steel – Tool
- Titanium
Composites
- Ceramics
- Insulation Materials
- Gasket Materials
- Kevlar
- Linoleum
- Mylar Laminates
- Neoprene
- Nylon
- Plexiglass
- Phenolics
- Poly Carbonate
- Polyethylene
- Polymers
- PVC
- Rubber
- Silicone
- Teflon
- Urethane
Other
- Cork
- Foam
- Glass – Decorative
- Glass – Bullet Proof
- Granite
- Hardwoods
- Leather
- Limestone
- Marble
- Quartz
- Tile – Ceramic
- Tile – Decorative
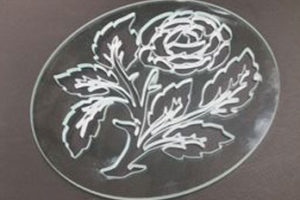
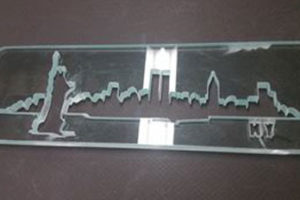
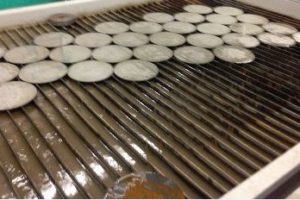
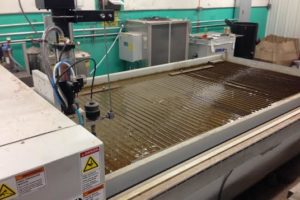
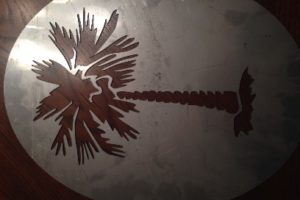